Plate-shaped Molybdenum Electrode In the glass furnace, compared with rod-shaped molybdenum electrode, plate-shaped molybdenum electrode has longer service life and service efficiency. However, due to technical limitations, plate-shaped molybdenum electrode connection mode is relatively simple. It usually punches at the center and links with heliciform lead electrode to fix by nut. But this installation method will increase the resistance between the electrodes and the lead electrode and for a period operation time the electrode is easy to loose, resulting in a series of damage. The worst case is the electrode can not be processed and can not be replaced.
Plate-shaped molybdenum electrode damage analysis during installation and operation: 1. The forging ratio of forged lead electrode is small so the grain in the molybdenum rod internal and external cross-section is uneven. In molten glass, the molybdenum grains continue to grow resulting in intergranular surface area to decrease and molybdenum rod strength to decline, so molybdenum lead electrode will fracture and molybdenum plate electrode will sink into the bottom. 2. Molybdenum plate electrode machining is rough and during the installation to tight molybdenum bolt and molybdenum nut too hard, causing damage to the root of the thread. 3. During cold charge, in order to prevent water glass (sodium silicate Na2SiO3) oxidation, ignore its corrosive effect Mo at high temperatures. 4. The mounting position of the electrode is too close to the pool tiles, caused pool tiles erosion. In electrochemical action, the various components of the molten glass, corundum, molybdenum will produce dark brown material dirty, contaminated liquid glass.
It can be seen, to extend the life of the electrode and improve its efficiency, which can improve the performance of the electrode material. Used powder metallurgy to produce La2O3-Mo electrode plate, the recrystallization temperature is higher than 1200 ℃ and has better mechanical properties. In addition, molybdenum lead electrodes and molybdenum bolt should produce by vacuum melting method, because compare to powder metallurgy method the products has higher high temperature strength resistance and can stand silicate, aluminum silicate solution erosion.
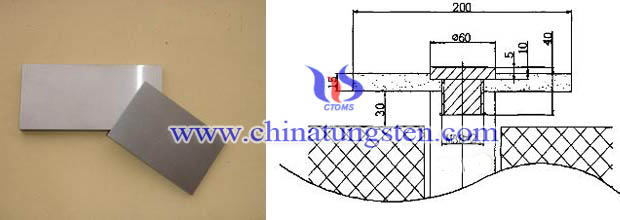
More details of the above news and/or products, please visit Chinatungsten Online, or contact us directly. Disclaimer: The article is only reflecting the opinions of the author. We have no responsibility to prove the originality and authenticity of the content, words and/or pictures. You readers should just take it as reference and check the details by yourselves. And the content is not a suggestion for investment decision. The investor takes his or her own risks if he or she operates accordingly. If you have any dissent about the contents above, please contact the relevant author, or the webmaster. We will try our best to assist the dealing of the related issues. Thanks for your visit and cooperation. |