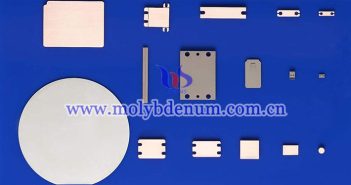
Molybdenum copper (Mo-Cu) tabs offer several advantages, making them highly valuable in various high-performance applications, particularly in electronics and thermal management systems. Here are the key advantages: 1. High Thermal Conductivity Efficient Heat Dissipation: The copper component in Mo-Cu tabs provides excellent thermal conductivity, allowing for efficient heat dissipation in electronic devices. This is crucial in preventing overheating and ensuring the reliable operation of high-power components. 2. Low Coefficient of Thermal Expansion (CTE) Dimensional Stability: Molybdenum has a low CTE,…